FREE-CUTTING STEELS
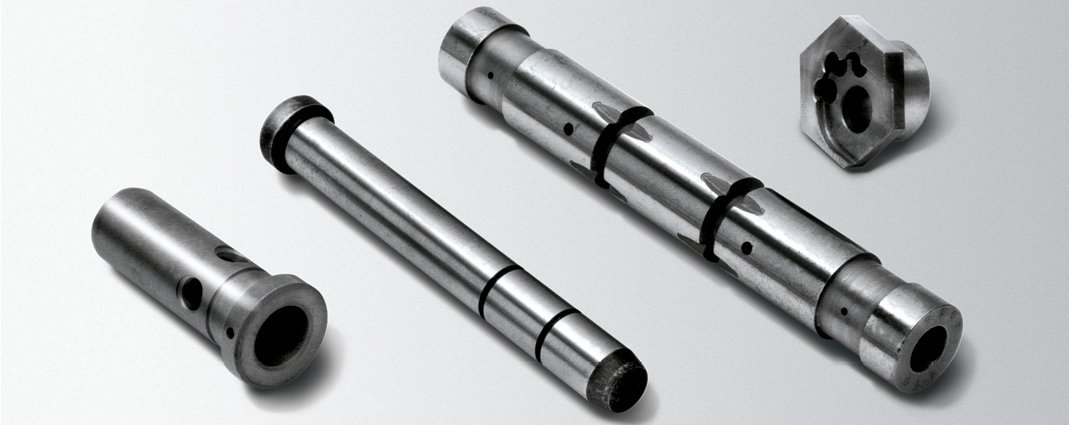
Free-cutting steels are characterized by a minimum quantity of S of 0.10%. There are 3 groups:
- not for heat treatment
- for case-hardening
- for quenching and tempering
Compared to the hot-rolled product, the cold-drawing condition offers tighter dimensional tolerances (more suitable for machining on automatic lathes) and absence of surface oxides which are harmful for the life of tools.
These steels offer excellent chip removal and are particularly suitable for large production volumes.
Lead has a very good lubrificating effect and, combined with the heating produced by teh tools, breaks chips thus allowing for higher productivity resulting in more advantageous production runs- It also guarantees lower tool wear. Lead does not have any influence on the mechanical features (longitudinally) of cold-processed steels, while it has been proved that it helps reduce up to 20% the fatigue limit of steels treated for R 1600 ÷ 1800 N/mm².
On the contrary, the use of lead worsens the steel’s mechanical features in the tangential direction, therefore designers will need to take this phenomenon into account by selecting more load-bearing sections. These steels are not suitable for the manufacture of gears, due to their lack of toughness in a transversal direction.
No negative aspects have yet been noted on case-hardened surfaces. On the other hand their better workability makes them suitable for use in the entire sector, where the high levels of hardness make the finishing operations more difficult.
Lead tends to refine the austenitic grain size, but does not worsen hardenability.
Leaded steels do not require different parameters than those commonly used for heat treatment, peeling, reeling, cold-drawing and grinding.
They allow for a machinability increase of up to 25-50%, depending on the type of steel used.
In free-cutting steels, the bench hardening obtained through cold-drawing favours chip removal.
Free-cutting steels are difficult to weld and whenever this operation is indispensable, the use of special electrodes is recommended to avoid cracking and porosity of the welding beads. In such cases the welded area shows a lack of lead which causes a reduction of machinability.
The most common fields of use are: starter motor shafts, fittings in general, brake couplings, hydraulics, lubricators, low-quality bearings, special screws, nuts, bolts, the furniture industry and small metal parts in general.