HEAT TREATMENTS
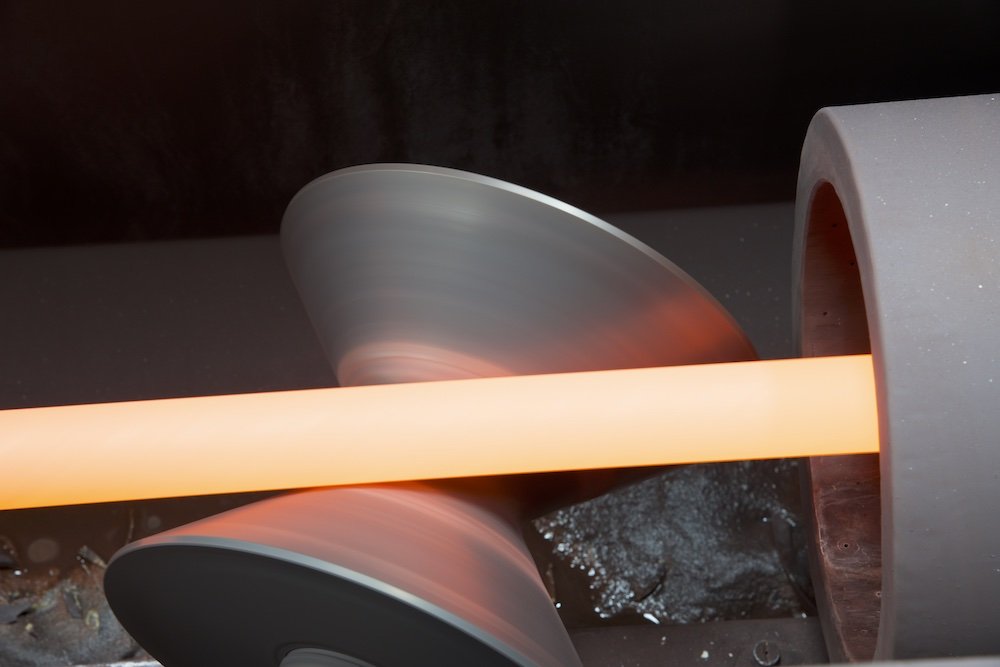
Our heat treatments:
- COILS: SUB CRITICAL ANNEALING IN PROTECTIVE ATMOSPHERE
- BARS: QUENCHING AND TEMPERING, STRESS-RELIEVING, ANNEALING, NORMALIZATION IN NON-PROTECTIVE ATMOSPHERE
- BARS: ANNEALING, NORMALIZATION, STRESS-RELIEVING IN PROTECTIVE ATMOSPHERE
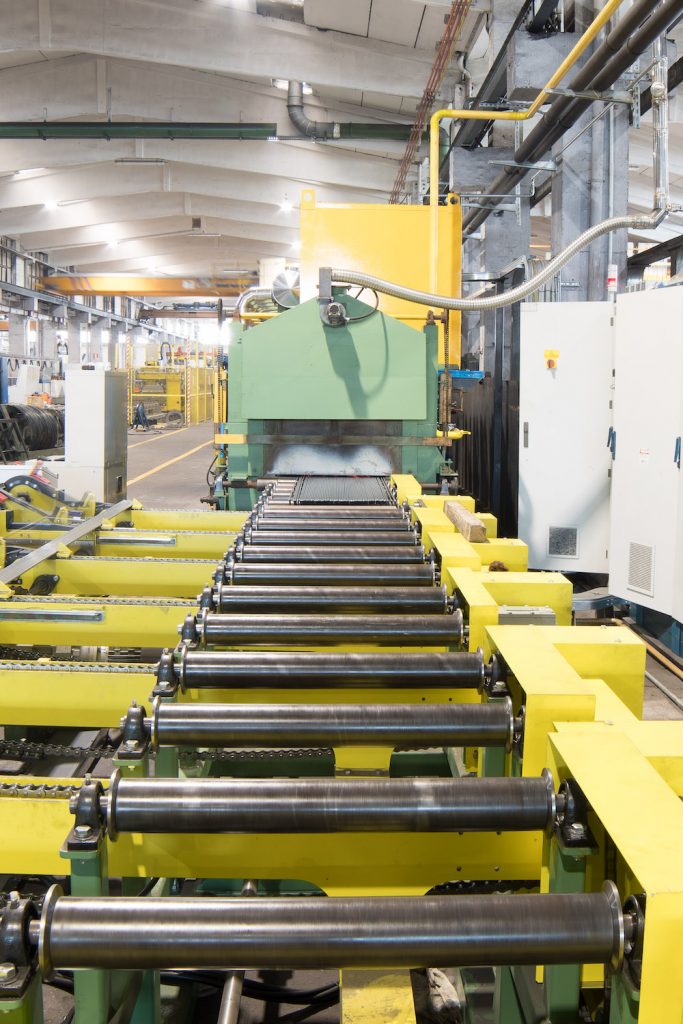
Generally, an appropriately selected and calibrated heat treatment, confers specific characteristics to steel products:
- mechanical and / or physical (hardness, breaking load and yield point, magnetic permeability, etc.);
- workability: cold plastic deformation and / or milling and machining;
- dimensional stability: in fact, as a result of classic manufacturing operations (welding, cutting, etc.) or due to the effect of operating conditions, undesired side effects, distortions and geometric variations may sometimes occur;
- micro-structural, for subsequent heat and / or thermo-chemical treatments
Heat treatments can be performed either on the finished piece (flange, valve, gear, etc.), or on the initial steel product (bar, tube, profile, sheet, etc.).
With regards to cold finished products supplied by the Lucefin Group, some heat treatments have an ever increasing importance and can be performed internally within the Group, thanks to its plant equipment:
- bell furnace for rolls (sub-critical annealing)
- induction furnace for bars (quenching and tempering, stress-relieving, annealing, normalization - in protective atmosphere)
- continuous furnace for bars (annealing, normalization, stress relieving – in a protective atmosphere.
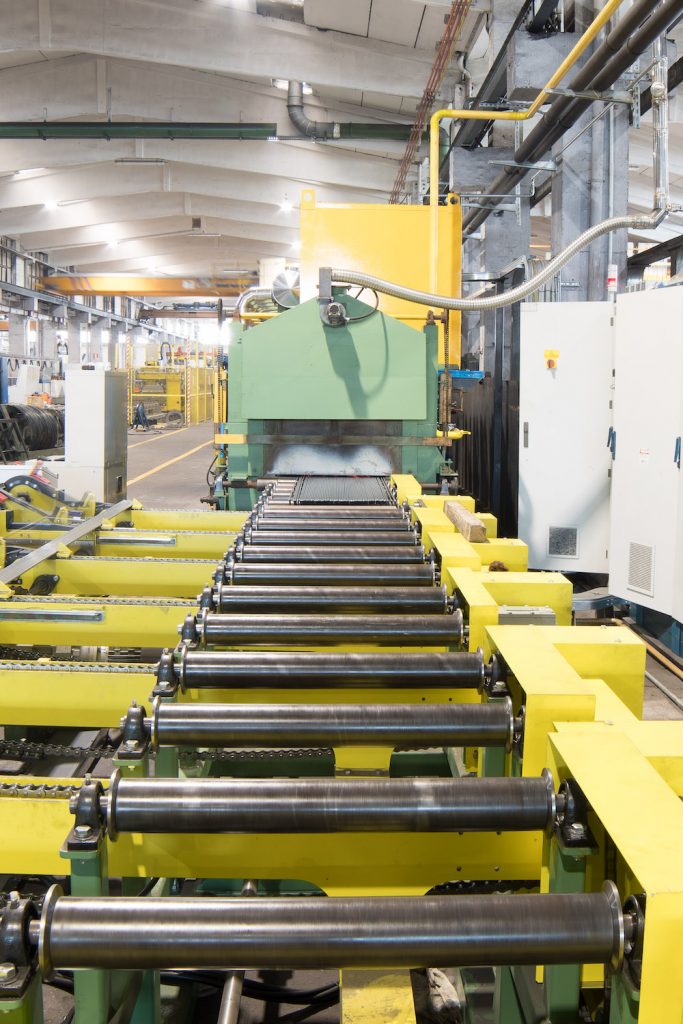
Generally, an appropriately selected and calibrated heat treatment, confers specific characteristics to steel products:
- mechanical and / or physical (hardness, breaking load and yield point, magnetic permeability, etc.);
- workability: cold plastic deformation and / or milling and machining;
- dimensional stability: in fact, as a result of classic manufacturing operations (welding, cutting, etc.) or due to the effect of operating conditions, undesired side effects, distortions and geometric variations may sometimes occur;
- micro-structural, for subsequent heat and / or thermo-chemical treatments
Heat treatments can be performed either on the finished piece (flange, valve, gear, etc.), or on the initial steel product (bar, tube, profile, sheet, etc.).
With regards to cold finished products supplied by the Lucefin Group, some heat treatments have an ever increasing importance and can be performed internally within the Group, thanks to its plant equipment:
- bell furnace for rolls (sub-critical annealing)
- tempering furnace for round bars (tempering, stress relieving, annealing, normalizing – in a non-protective atmosphere) normalization - in protective atmosphere)
- continuous furnace for bars (annealing, normalization, stress relieving – in a protective atmosphere.
The European (EN) and International (ISO) regulations have also acknowledged the growing importance of heat treatments on cold finished bars: the new EN 10277 and ISO 683-18, consider the possibility of supplying cold finished products (drawn, peeled and ground) with specific heat treatment: in particular, specific indications have been introduced for those subjected to stress relieving, annealing and normalization after drawing:
- drawn and stress relieved (+C+SR)
- drawn and annealed (+C+A)
- drawn and normalized (+C+N)
Besides these, there are other products that have already been mentioned in the product standards and are supplied by the Lucefin Group, namely:
- annealed and drawn (+A+C)
- annealed and peeled (+A+SH)
- tempered (+QT): after drawing (+C+QT), before drawing (+QT+C), peeled / rolled (+QT+SH) (+QT+SH)
Below is a brief description of the main effects that the above mentioned thermal treatments have on the drawn product and, where indicated, also on the peeled product (the rectified products obtained from drawn and peeled processes “inherit” the characteristics of the same, because the drawing process does not change the mechanical or micro-structural characteristics).
STRESS RELIEVING (+SR)
Following the stress relieving treatment, there is a general reorganization of the internal tensions of the material, with partial recovery of the ductility. The mechanical characteristics do not undergo particularly important variations and the microstructure of the material is fundamentally unchanged.
The aforementioned rearrangement of the internal stresses and the partial recovery of ductility give the material a good dimensional stability avoiding distortions after subsequent processing, as well as allowing a greater aptitude for cold plastic deformation operations (e.g. bending).
ANNEALING
Workability annealing (+A)
Recrystallization annealing (+RA)
The main effect is a reduction of the effects of cold plastic deformation (work hardening and residual stresses): the microstructure undergoes a general morphological reorganization that involves an optimal recovery of the cold plastic deformability characteristics and is therefore suitable for those products that will be subjected to operations such as bending, upsetting, etc.
Magnetic annealing (soft-annealing) (+A)
This is an annealing treatment aimed at achieving specific values of the magnetic parameters of the material, ie coercive force (Hc) and and the magnetic permeability (µr)
For all types of annealing, the mechanical characteristics vary in the sense of a reduction in hardness, breaking (Rm) and yield strength (Rm e Rp0,2%) and with an increase in elongation percentage at break point (A% ) and rupture percentage at fracture (Z%).
Workability annealing (+A)
Recrystallization annealing (+RA)
The main effect is a reduction of the effects of cold plastic deformation (work hardening and residual stresses): the microstructure undergoes a general morphological reorganization that involves an optimal recovery of the cold plastic deformability characteristics and is therefore suitable for those products that will be subjected to operations such as bending, upsetting, etc.
Magnetic annealing (soft-annealing) (+A)
This is an annealing treatment aimed at achieving specific values of the magnetic parameters of the material, ie coercive force (Hc) and and the magnetic permeability (µr)
For all types of annealing, the mechanical characteristics vary in the sense of a reduction in hardness, breaking (Rm) and yield strength (Rm e Rp0,2%) and with an increase in elongation percentage at break point (A% ) and rupture percentage at fracture (Z%).
NORMALIZATION
It is a high temperature heat treatment that involves a complete transformation of the starting microstructure, with complete cancellation of the effects of previous workings. Consequently, after normalization the product presents:
- low mechanical characteristics
- excellent characteristics of cold plastic deformability
- maximum dimensional stability
- microstructural homogeneity (absence of lamination bands and chemical inhomogeneities)
- mechanical isotropy: the mechanical characteristics are independent of the product orientation as the microstructure is homogeneous
- optimal for any subsequent particularly demanding tempering treatments
TEMPERING
Tempering is actually the combination of two complementary thermal treatments, namely QUENCHING + TEMPERING.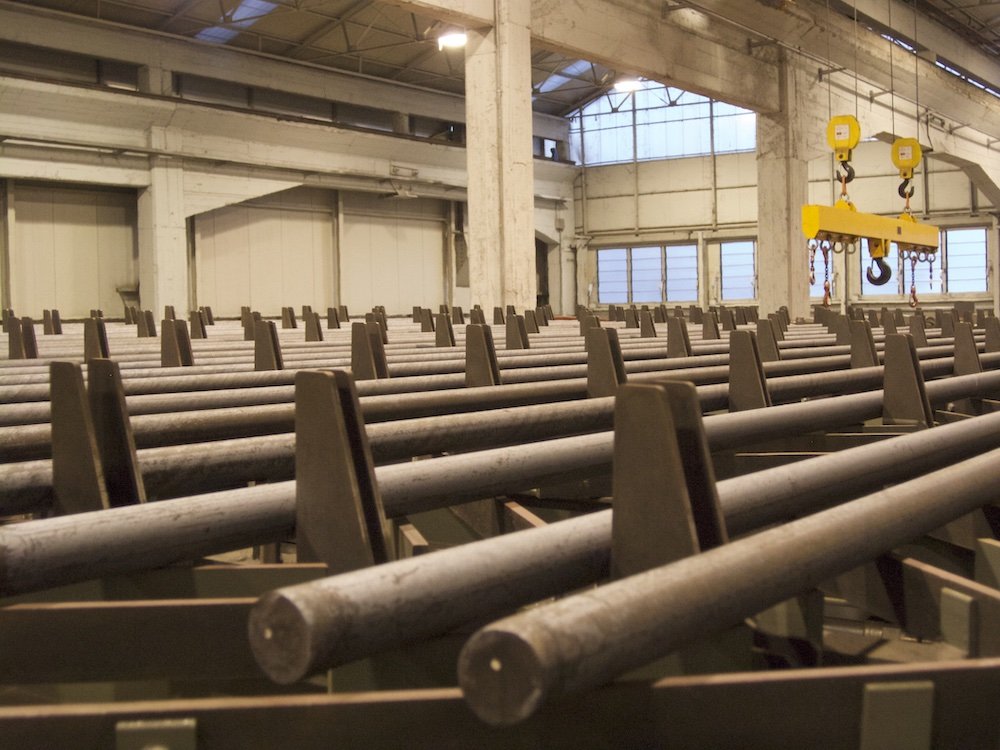
Quenching
This is a heat treatment that, due to drastic cooling after reaching specific temperatures, induces the formation of the so-called MARTENSITE in the steel, structural constituent characterized by: high breaking load, yield strength and hardness, but of low toughness and ability to cold deformation, as well as quite strong residual stresses.
Tempering
Tempering allows the partial recovery of ductility and the attenuation of residual stresses after quenching; the greater the temperature at which this occurs, the greater the recovery of ductility of the material and the reduction of hardness and of the breaking and yielding loads reached during hardening.
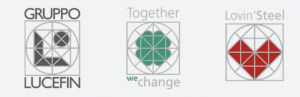
© 2025 All rights Reserved – LUCEFIN S.P.A. via Ruc 30 Esine (BS) ITALY P.IVA IT01535340986 – lu*****@*******il.it – co*****@*****in.com