STAINLESS STEELS
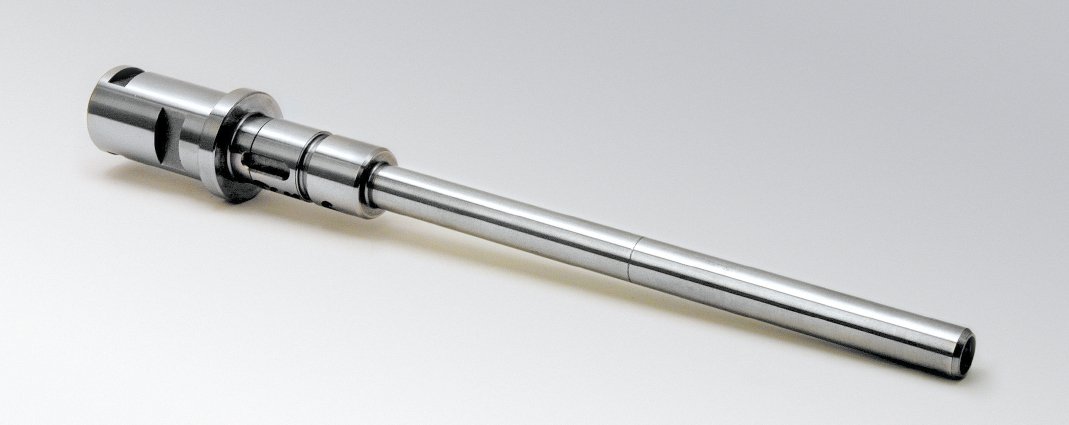
Stainless steels contain a high percentage of chromium and sometimes other alloys and have been designed to prevent different types of corrosion. There are two kinds of corrosion: dry corrosion (often named high-temperature corrosion or oxidation) and wet corrosion, which can be observed in liquid environments (or when the metal becomes coated with liquid condensate).
The hot corrosion resistance of stainless steels is connected with the creation of a thin and adherent passive surface layer, which avoids further attack against the material.
The wet corrosion process is by contrast an electrochemical process and the corrosion resistance of stainless steels is due to the formation of a passive surface layer which, in order to take shape, requires a chromium content of about 12%. The formation of this “passive” state deeply changes because of various factors such as steel type, its chemical composition, material state, test treatment conditions, surface finishing, etc. For each type of stainless steel this layer has to be continuous and adherent to the surface, non-porous and insoluble, able to recover itself every time it breaks down if exposed to air or to the action of oxidizing environments.
The structure of these metallic materials determines their classification into the following groups: ferritic, martensitic, austenitic, austenitic-ferritic and precipitation hardening.
Ferritic steels.These steels have no critical points and their structure is guaranteed by a low carbon content and a high percentage of chromium. They have a good heat resistance and are suitable for oxidizing environments. They are used event at ambient temperature. Their toughness drops considerably at low temperatures. They do not have critical points and are not, therefore, susceptible to hardening. They are normally used in a recrystallizing annealed state.
Martensitic steels.Their name comes from the fact that they are the only stainless steels that have critical points (Ac1, Ac3) and therefore, after hardening, they adopt such a structure. Because of the chromium presence both the isotherm and anisotherm curves shift towards the right and for this reason the martensitic structure can also be obtained through air cooling. As for the steels for quenching and tempering, their best properties can be obtained after quenching and tempering treatment; it is very important to pay attention to this last treatment because of the precipitation of chromium carbides that can alter their corrosion resistance.
Austenitic steels.The austenitic structure is stable at ambient temperature thanks to the simultaneous presence of chromium and nickel together with the low carbon content. They are the most commonly used in several aggressive environments, at low and high operating temperatures. Solubilization is their usual heat treatment state. The use of cold-drawn steel bars is very common because this cold process gives the desired bench hardening, enhancing the resistance characteristics. In order to facilitate cold processing and to avoid exceeding the work hardening, oxalating treatments are carried out in order to form “bearings” between the metal surface and the dies, thereby reducing friction to a minimum. The mechanical resistance may also be increased through the addition of nitrogen and molybdenum. A smooth and uniform surface, with an extremely low roughness value considerably increases their corrosion resistance.
Austenitic/Ferritic steels.These products, which are commonly known as duplex steels, contain chromium, nickel, molybdenum, nitrogen and, in some cases, have a two-phase structure, made up by austenitic islands in ferritic matrix more or less in the same number. The main characteristic of these steels are excellent corrosion strength under stress and a high yield point.
Precipitation hardening steels.These steels are for the PH (Precipitation Hardening) series. Hardening is achieved by means of subsequent reheating at temperatures which are not very high (480-600 °C). Their main characteristic is the quite good corrosion resistance, coupled with excellent mechanical properties. The elements mainly used to harden these steels are: titanium (T), niobium (Nb), nitrogen (N), aluminium (Al), copper (Cu). This category also includes martensitic, austenitic and half-austenitic steel types. Due to their high cost, their use is essentially limited to sectors such as aerospace and energy production, which require a high resistance and excellent elongation.
The most common stainless steels are:
AISI 303 – AISI 304 – AISI 316 – AISI 416 – AISI 420 – AISI 430 – AISI 431