TOOL STEELS
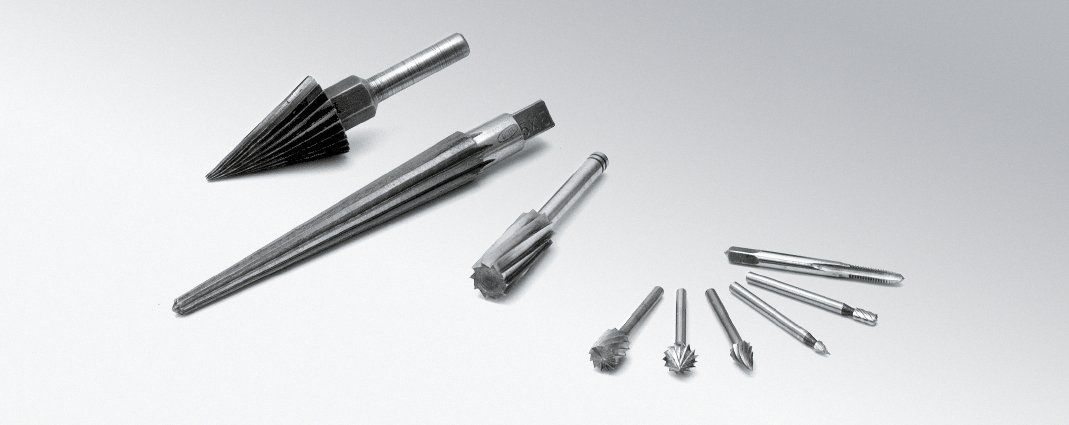
Hot-work tool steels
This category of steels must have special characteristics: resistance to non-continuous heat (450-600 °C) and insensitivity to coarsening which happens when the material is exposed to high temperatures for long periods of time.
For special uses, where temperatures can reach 600 °C, the steels normally contain also a high percentage of tungsten (18%).
They are used for high-pressure dies and pipes expanders.
Nickel-chrome-molybdenum-vanadium steels have good toughness even when hot and resist well to heat variations and tempering.
The main enemies for the productivity of dies have always been wear, failure and maintenance work, therefore close contact between manufacturer and customer is needed to agree upon and optimise costs and quality.
Cold-work tool steels
The particular characteristic of these steels is their high carbon content, which gives the tools a high level of hardness. Their use tends to be concentrated in those sectors in which wear, impact and shear stresses are present. Their main characteristics are: hardness, toughness, wear resistance and hardenability. The hardness of steels for cold work varies from 52 to 63 HRC, whilst the hardness for hot-work steels ranges from 36 to 54 HRC. Selection of the most suitable type of steel for a specific purpose is not easy and should be carried out after accurate appraisals.