NITRIDING STEELS
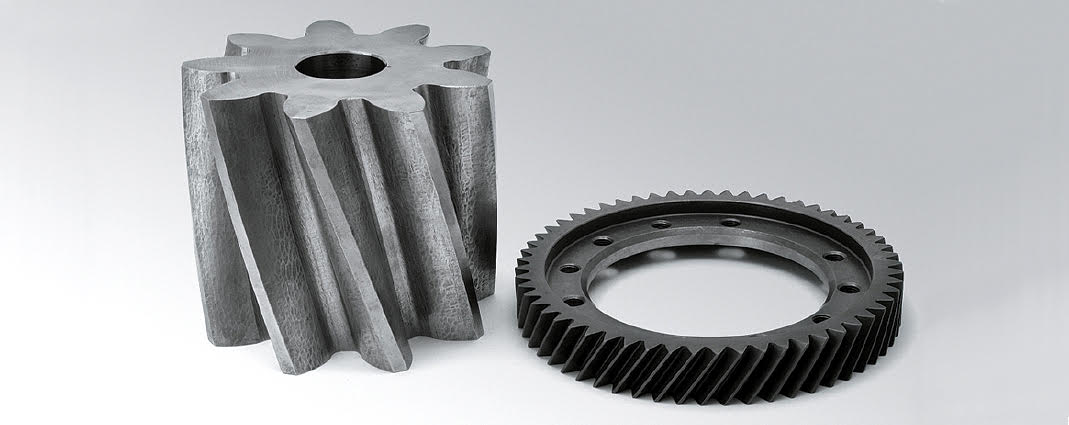
Nitriding steels are normally supplied in hot-rolled or forged form, either in annealed or quenched and tempered condition. The quenching and tempering gives the base material excellent strength and impact resistance values, while the surface nitriding treatment is used to achieve wear resistance. This treatment delivers even greater surface hardness than that which can be obtained with case-hardened steels.
The particular characteristic of nitrided steels is their high friction resistance, even up to 500 °C. Consequently, in machine parts where lubrication is not good, the chafing effect does not cause great damage, contrary to what could happen with case-hardened parts. Another characteristic is their high resistance to sea water and steam.
This treatment is carried out in furnaces at controlled temperatures and with a perfect seal, since harmful oxidation could occur in contact with air. The main component for this operation is a uniformly distributed ammonia gas mixture. A quenching and tempering heat treatment is recommended on the rough-shaped material absolutely free of stresses, followed by polishing, cleaning, drying, nitriding and final grinding.
Nitriding normally penetrates approximately 0.1 mm every 12 hours at a temperature of 510 °C and for the first 0.03 mm (white layer) the hardness does not reflect the true hardness. It is therefore necessary to use instruments such as the Rockwell diamond cone in order to overcome this layer or to remove at least 0.03 mm.
The major field of use is for the plastic extrusion sector, screws and plasticizing chambers. Other uses are eccentric shafts, discs, injection pumps, plugs and steam distribution chambers.
The most common nitriding steels are: